Keeping Cool in a GT40
Putting AC in a car like this is considered by some a luxury. However it becomes a necessity if driving the car on the road is to be an enjoyable experience. With a great deal of AC experience this part of the build was going to be a little special.
Installing a capable AC system in a car with limited space is always going to be a challenge. In order to make the best use of the space available in the cabin a custom system was manufactured.
The starting point was a good SPAL brand blower motor. Next was to procure a good aftermarket evaporator case and cut it to bits! A fiberglass transition duct between the blower and evaporator case was made so that the unit could tuck under the dash and not impact the passenger foot-well area. The blower to was positioned in a triangular portion of the passenger side within the under dash structure.
You can see the process of positioning the blower to fit in the vehicle below. Temporary "sticks" aligned the blower and evaporator. A fiberglass duct was then constructed to create an air duct.
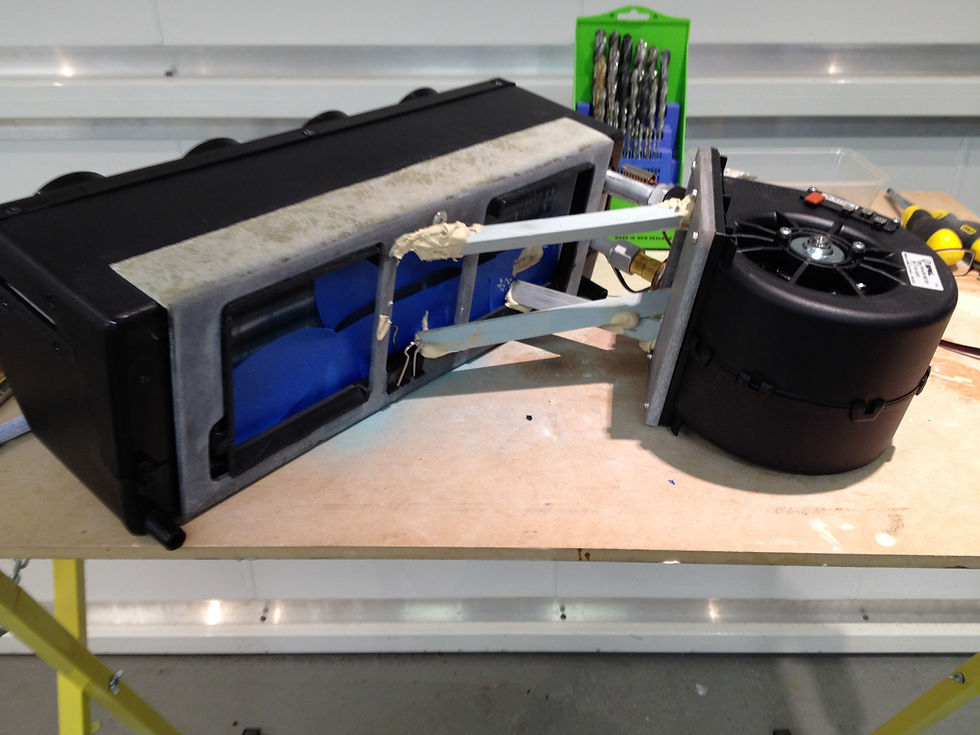
The fiberglass sheets used for this were made by sandwiching resin and matting between two panes of glass.

Once painted the result is well worth the effort.

The system included the drainage system for condensate and positioned the TX valve in a position that allowed the plumbing to route in a way that made installation and removal of the system possible.

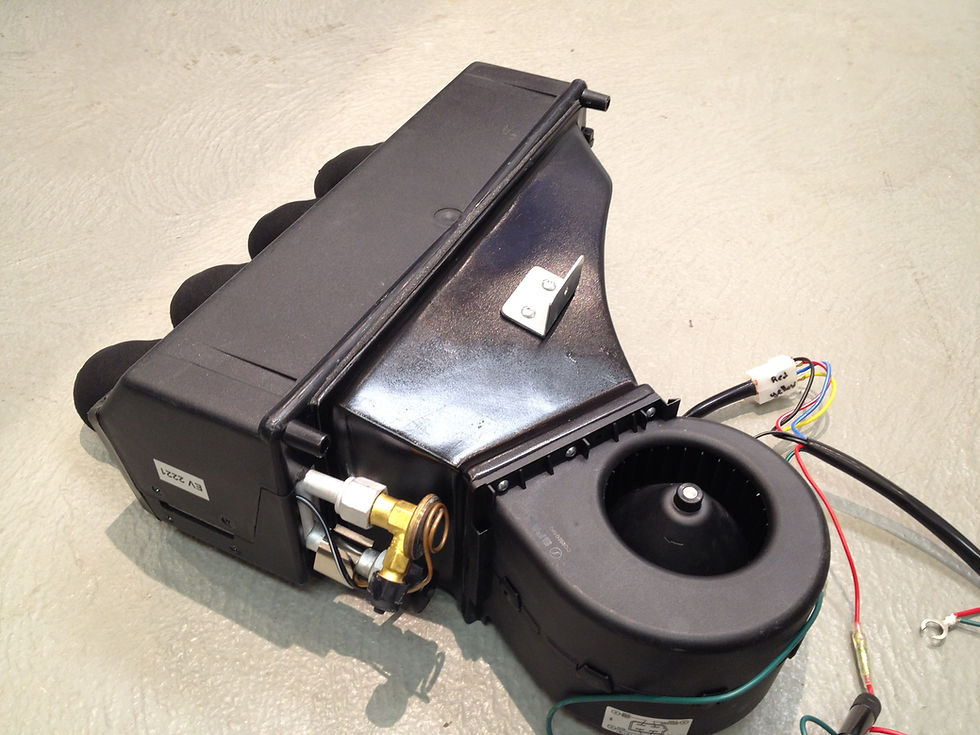
A plenum chamber for the evaporator to blow into and distribute the air to the side vents and center dash outlet was next. This was also made out of fiberglass.

This duct was designed to ensure the dash duct aligns with the air delivery system as the dash is installed. This allows the dash to be removed without having to disconnect hoses etc.

The under dash duct was then insulated to keep the air cool and stop the formation of condensate.
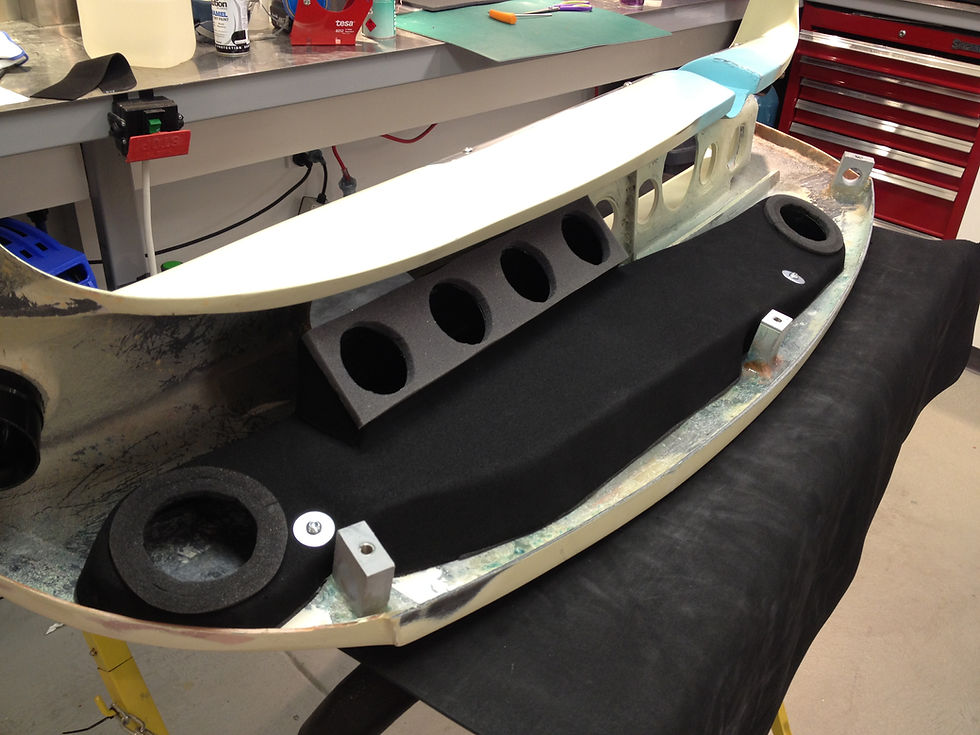
Next task was to fit the AC compressor. As can be seen the OE compressor was never going to fit.
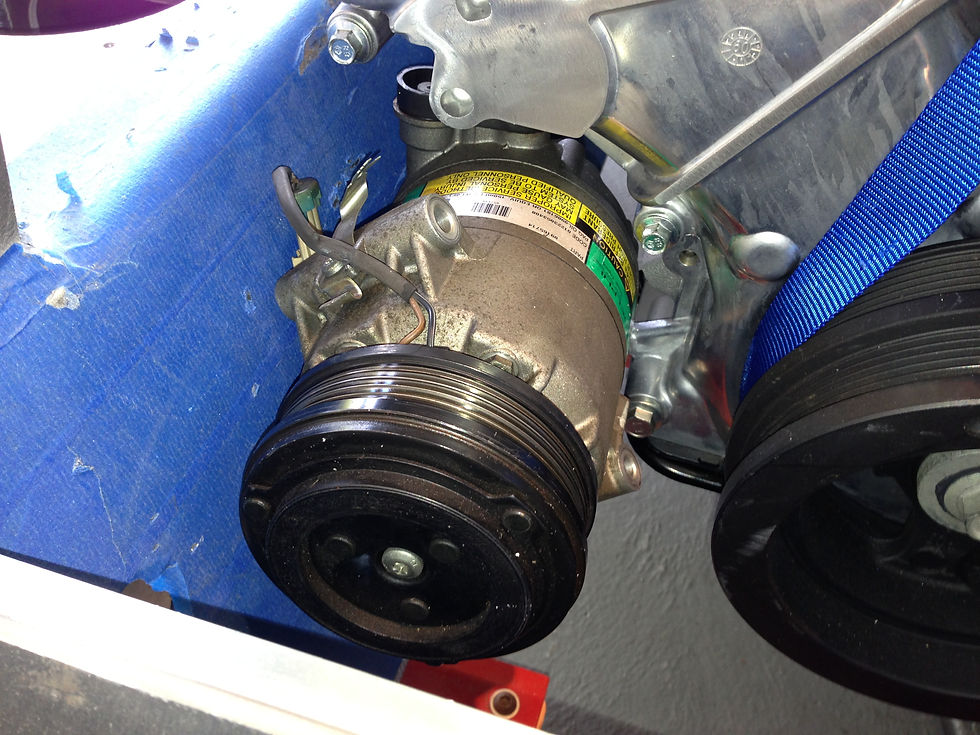
So a custom solution was required. A great compressor that is both small in size and capable of delivering excellent performance was found. An old one was used for a positional mock up.
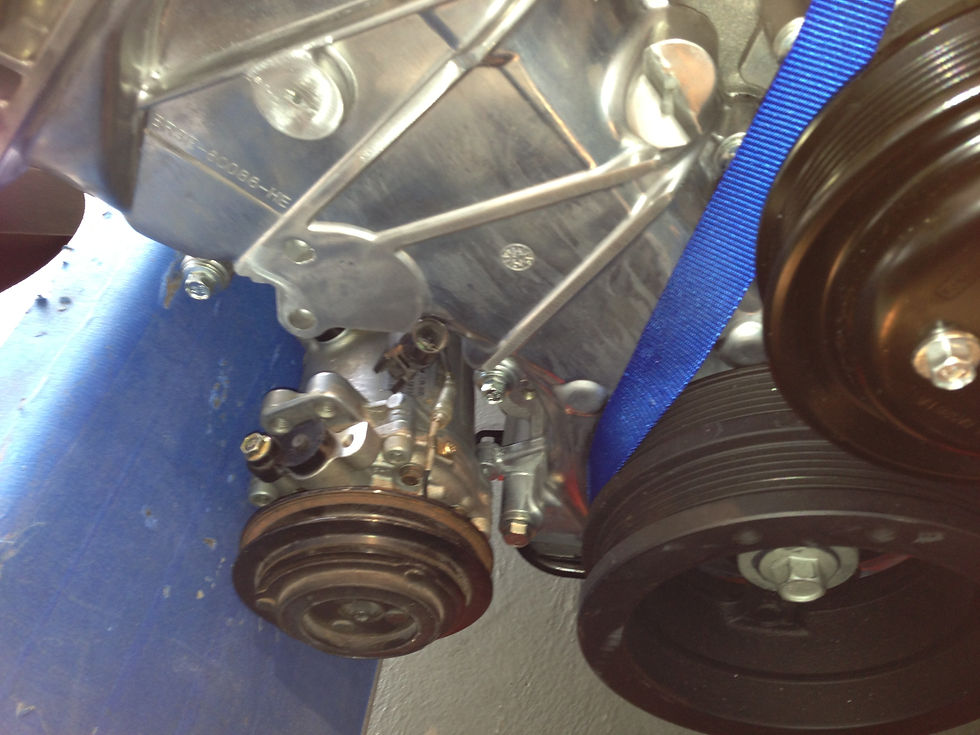
A custom drive belt system was required due to the non-standard AC compressor and alternator position.

This made new layout made fitting the compressor possible. This also allows the use of one belt to run all the accessories.

Keeping the pulley gauge line perfectly aligned is critical to ensuring reliable operation of the entire system.

The refrigerant plumbing was then completed in aluminium hard tube. The only hose used is at the compressor and evaporator interface. Minimising the length of hose in an AC system contributes to reduced refrigerant permeation (leakage) as well as reduced weight. Lastly to control the system a refrigerant pressure transducer was installed to provide the Haltec ECU with the information necessary to protect the system from high and low pressures. A basic trinary switch could be used however this is a far more elegant solution.
Comments